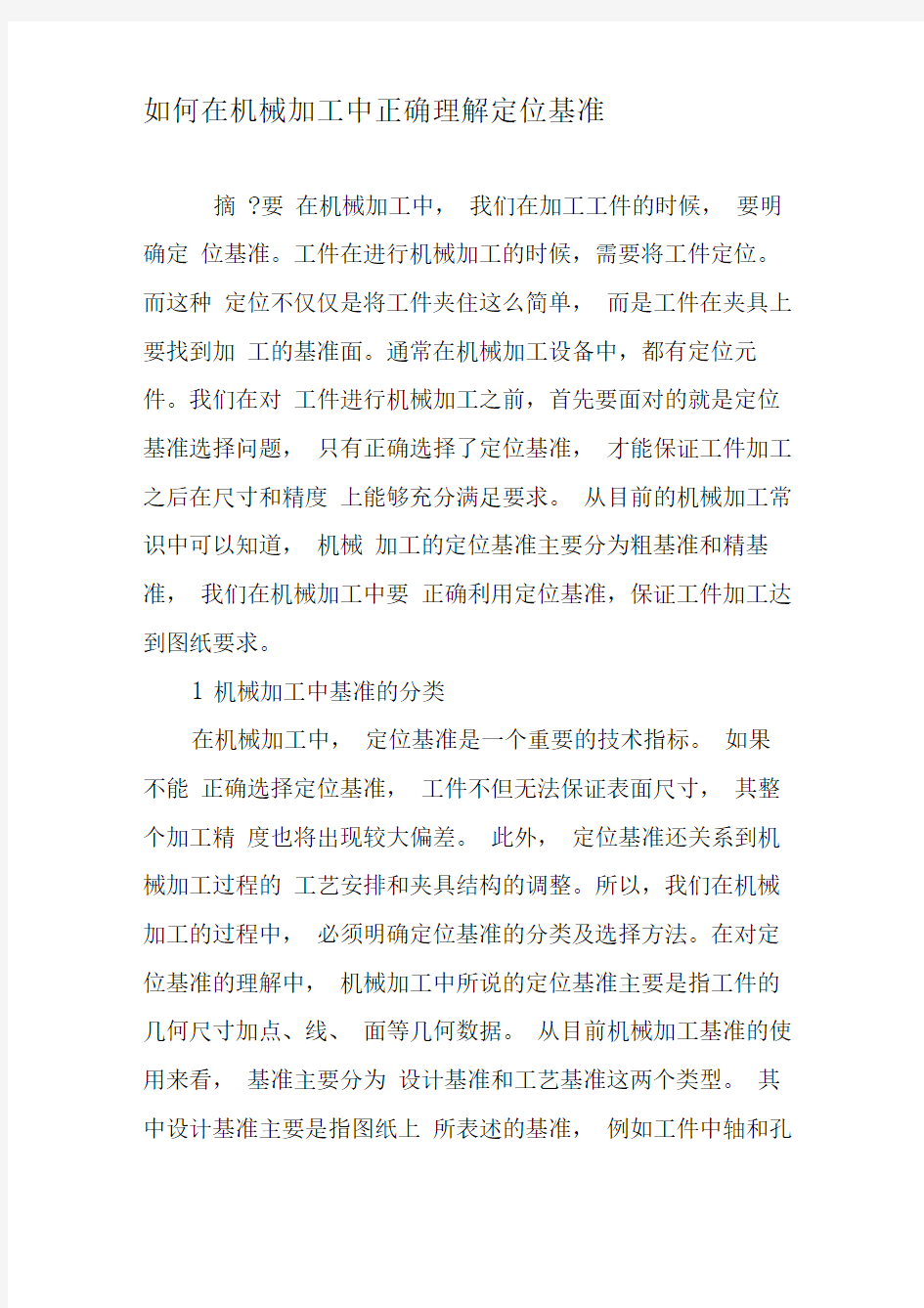
如何在机械加工中正确理解定位基准
- 格式:docx
- 大小:9.13 KB
- 文档页数:6
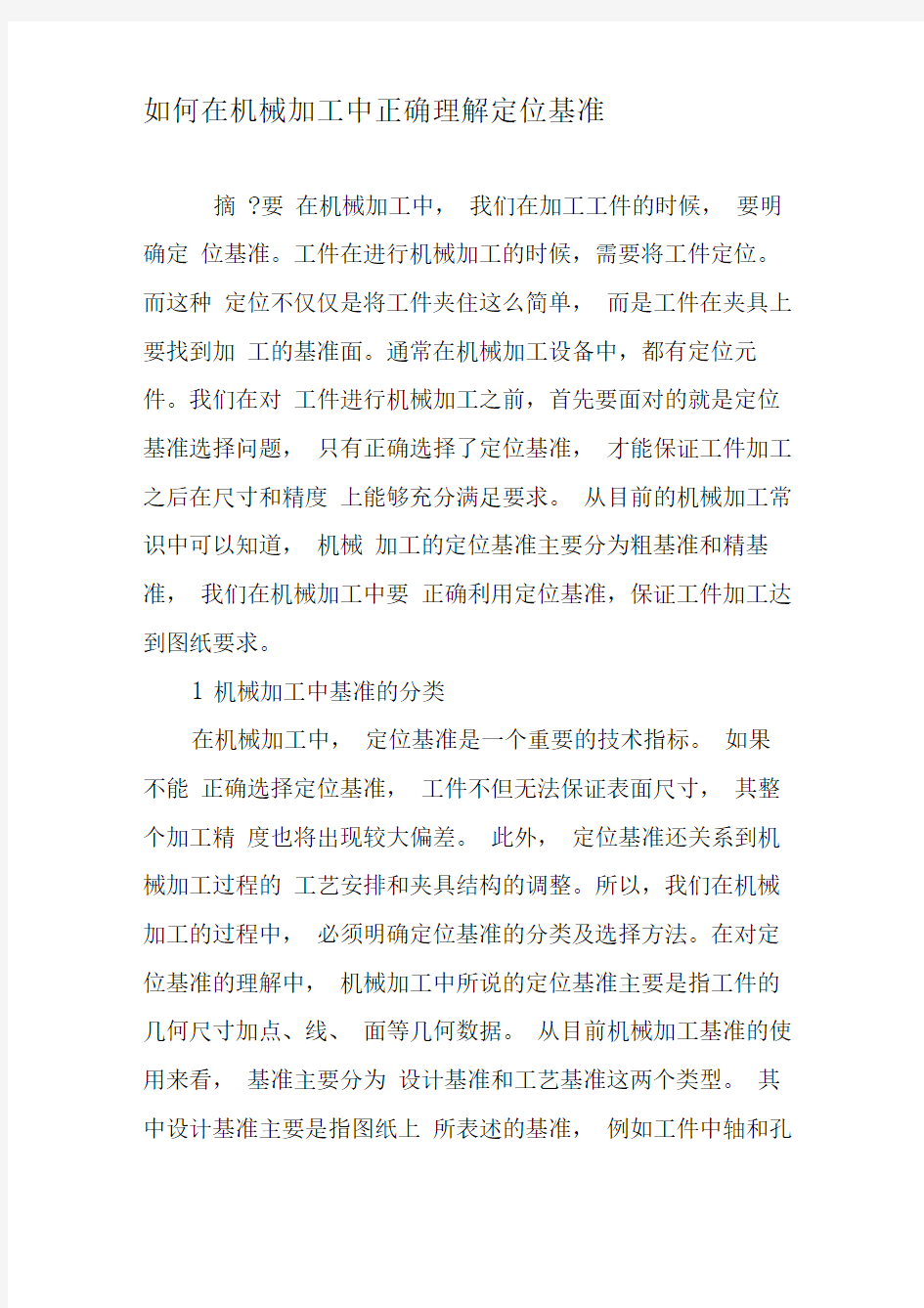
如何在机械加工中正确理解定位基准
摘?要在机械加工中,我们在加工工件的时候,要明确定位基准。工件在进行机械加工的时候,需要将工件定位。而这种定位不仅仅是将工件夹住这么简单,而是工件在夹具上要找到加工的基准面。通常在机械加工设备中,都有定位元件。我们在对工件进行机械加工之前,首先要面对的就是定位基准选择问题,只有正确选择了定位基准,才能保证工件加工之后在尺寸和精度上能够充分满足要求。从目前的机械加工常识中可以知道,机械加工的定位基准主要分为粗基准和精基准,我们在机械加工中要正确利用定位基准,保证工件加工达到图纸要求。
1机械加工中基准的分类
在机械加工中,定位基准是一个重要的技术指标。如果不能正确选择定位基准,工件不但无法保证表面尺寸,其整个加工精度也将出现较大偏差。此外,定位基准还关系到机械加工过程的工艺安排和夹具结构的调整。所以,我们在机械加工的过程中,必须明确定位基准的分类及选择方法。在对定位基准的理解中,机械加工中所说的定位基准主要是指工件的几何尺寸加点、线、面等几何数据。从目前机械加工基准的使用来看,基准主要分为设计基准和工艺基准这两个类型。其中设计基准主要是指图纸上所表述的基准,例如工件中轴和孔
的中心线等。工艺基准主要是指在机械加工工艺过程中所使用的基准。主要有定位基准、测量基准和装配基准等几种类型。其中定位基准是最基础的基准,对工件的加工精度有着重要影响。
2粗基准的选择原则
工件在进行机械加工之前,所有的面都处于毛坯状态,
在这种状态下,要想实现对工件的准确定位并确定加工面,就要以工件的某一毛坯面为定位基准。通常我们称这种方式确定的定位基准为粗基准。我们在选择确定粗基准的时候,要想使粗基准达到要求,就要做好两方面的工作,一方面是要使工件的加工面和不加工面之间的位置和精度达到要求,另一方面是要确定合理的加工余量,保证加工精度达到要求。在工件机械加工粗基准的选择中,主要应遵循以下原则。
2.1以工件不加工的表面作为粗基准
在工件上选择粗基准的时候,通常我们会选择不加工的表面作为粗基准,这主要是因为工件有时并不是所有的面都需要加工,总有一到两个面不需要加工,我们选择不加工的表面作为粗基准的时候,可以保证定位基准的有效性。在工件的实际机械加工过程中,我们要保证工件加工面和不加工面的相互位置和尺寸满足规定要求,使粗基准起到定位基准的作用。一旦遇到工件的所有表面都需要加工的时候,我们就要选择表面加工余量最小的表面作为粗基准,这样选择的目的主要是保
证其他加工面能够有充足的余量。所以,我们在选择粗基准的时候,应首选工件不加工的表面。
2.2合理选择加工余量,以工件的均匀的重要表面为粗基准在机械加工过程中,我们对工件加工的时候,要合理选择加工余量,既要保证加工余量满足加工要求,又要保证加工余量能够满足后续加工的需要。同时,我们应以工件的均匀的重要表面为粗基准,保证工件定位基准的有效性。我们在选择工件定位基准的时候以工件的均匀的重要表面为粗基准,主要是考虑到工件的均匀的重要表面符合粗基准的特征,作为粗基准能够起到规范基准,满足加工精度需要。在工件的均匀的重要表面选择为粗基准的时候,工件的均匀的重要表面的加工余量要保证均匀,这样才能保证工件在后续的加工中能够满足精度要求。通常利用这种原则选择的粗基准,能够满足加工要求。
2.3粗基准的选用只能使用一次,不能反复使用我们在机械加工中合理选择粗基准是满足加工要求的具体体现,但是我们也要清楚,粗基准在同一个工件上的选用只能使用一次,不能反复使用。这主要是因为误差要求。由于粗基准是起始加工工序中选择的未加工表面进行定位的,定位精度低,所以同一方向上,粗基准只允许使用一次,以免定位误差太大。另外,用作粗基准的表面尽可能光洁、平整、有足够的面积,以减少定位误差,使工件装夹稳定。接下来的加工工序中,则是考虑
精基准的选择了。所以,我们要清楚工件机械加工中工件粗基准的选择原则,做好粗基准的选择工作,保证工件的定位基准能够达到要求。
3精基准的选择原则
在机械加工中,除了粗基准的选择以外,我们还要做好精基准的选择。通常在机械加工中,精基准主要是指在定位基准的选择上,以已加工的表面作为定位基准。我们在精基准的选择上,应该从保证工件加工精度这一角度出发,还要兼顾工件安装和夹固的牢固程度。从目前机械加工定位基准的选择来看,我们在选择精基准的时候,要遵守以下原则。
3.1 保证设计基准与精基准重合
以设计基准作为精基准,称为基准重合原则。基准重合原则可以避免因基准不重合引起的误差,特别是对于零件的最后精加工工序,更应遵循这一原则。常见的是机床主轴锥孔的最后精磨加工工序,应选择支承轴颈来定位。在实际的机械加工过程中,保证设计基准与精基准重合,可以有效减少机械加工带来的误差,使加工精度更准确,更能满足实际需要。在目前的机械加工中,普遍采用了设计基准与精基准重合的方式,使工件的加工精度得到了可靠的提高。
3.2 保证定位基准的统一性选择统一的定位基准加工工件上的各个加工表面,避免基准转换带来的误差,称为基准统一原则。采用统一基准原则加工工件各表面,有利于保证各
表面的相互位置要求,而且还能简化夹具设计和制造,缩短生产准备周期。保证定位基准的统一性,能够使工件的各个加工表面在机械加工中有统一的基准可以遵循,使每个加工表面的加工精度和加工质量能够有同一标准来衡量。在目前机械加工过程中,定位基准的统一性得到了很好的利用,取得了积极的效果。
3.3采用自为基准为精基准的方式选择加工表面本身作为精基准进行定位,称为自为基准原则。通常这样的加工表面精加工要求余量小而均匀。自为基准可提高加工面本身的精度和表面质量。自为基准的采用,主要是考虑到工件在加工过程中,个别加工面存在特殊的要求,无法用统一的标准来要求。在这种状况下,就需要采用自为基准为精基准的方式来确定工件的定位基准。从目前的实际加工过程来看,采用自为基准为精基准的方式以后,对工件的加工表面精加工取得了预期的效果,达到了预期要求。3.4 采用互为基准为精基准的方式
以零件上重要表面互为基准反复进行加工,称为互为基准原则。互为基准原则主要用于精密零件的加工,提高重要表面间的相互位置精度。互为基准的概念主要是相对于自为基准而言的,采用了互为基准的精基准以后,工件在加工的过程中可以对不同的表面采用不同的基准进行加工,并保证了工件的重要表面上的基准可以根据实际需要随时变化,保证了加工精度